Dall'Artigianato al Digitale: Come il Software Su Misura sta Rivoluzionando l'Industria 4.0
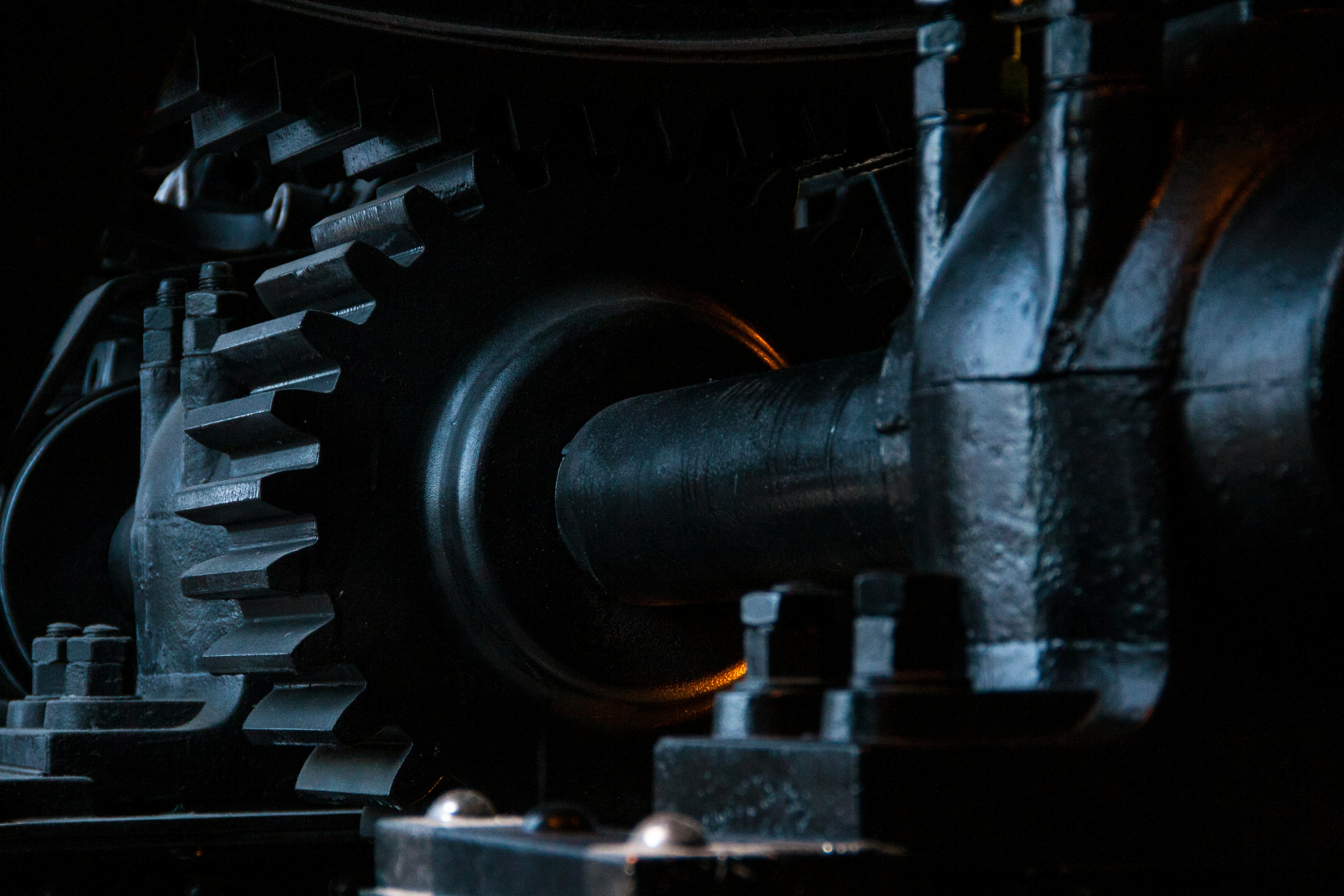
Introduzione
L'industria manifatturiera ha subito profonde trasformazioni nel corso della storia, passando dalla produzione artigianale all'automazione spinta. Oggi stiamo assistendo alla quarta rivoluzione industriale, conosciuta come Industria 4.0, che rappresenta una nuova frontiera della digitalizzazione della fabbrica.
Il concetto di Fabbrica Digitale fa riferimento all'integrazione di tecnologie digitali nei processi produttivi, come l'Internet of Things, il cloud computing e l'intelligenza artificiale. L'obiettivo è creare impianti sempre più interconnessi e smart, in grado di raccogliere ed elaborare una grande mole di dati per ottimizzare le operazioni.
L'Industria 4.0 porta la Fabbrica Digitale a un livello superiore, puntando a una completa digitalizzazione dell'intera catena del valore. Non si tratta solo di rendere più efficienti i singoli impianti, ma di trasformare l'intero modello produttivo e distributivo grazie alle tecnologie abilitanti. I principi cardine sono l'interoperabilità, la virtualizzazione, la decentralizzazione, la capacità in tempo reale e l'orientamento al servizio.
La Prima Rivoluzione Industriale
La prima rivoluzione industriale ebbe inizio alla fine del XVIII secolo ed è associata all'invenzione del motore a vapore e delle macchine tessili. Queste innovazioni portarono ad una radicale trasformazione della produzione manifatturiera, con il passaggio dalla manifattura artigianale alla produzione meccanizzata su larga scala.
L'introduzione delle macchine a vapore, come la macchina a vapore di James Watt, permise di sostituire la forza animale e idraulica con una fonte di energia più potente e affidabile. Le macchine a vapore vennero utilizzate per azionare i telai meccanici nell'industria tessile e successivamente trovarono applicazione in molti altri settori.
La disponibilità di energia a basso costo diede impulso alla costruzione delle prime fabbriche, con grandi quantità di operai che lavoravano contemporaneamente con macchinari alimentati a vapore. Si assistette così ad una produzione di massa, standardizzata e a costi decrescenti.
La prima rivoluzione industriale portò quindi ad una profonda trasformazione economica e sociale, con l'affermazione del capitalismo industriale e la nascita della classe operaia su larga scala. Il paesaggio urbano fu radicalmente modificato dalla costruzione di fabbriche e infrastrutture. In sintesi, il motore a vapore e la meccanizzazione segnarono l'inizio dell'era industriale moderna.
La Seconda Rivoluzione Industriale
La seconda rivoluzione industriale ebbe inizio alla fine del XIX secolo ed è caratterizzata principalmente dall'introduzione dell'elettricità e della catena di montaggio.
L'elettrificazione delle fabbriche permise l'utilizzo di macchinari più potenti ed efficienti rispetto al vapore, portando ad una maggiore produttività. Inoltre, l'illuminazione elettrica consentì di estendere il lavoro anche nelle ore notturne.
Ma il vero salto in avanti si ebbe con l'invenzione della catena di montaggio da parte di Henry Ford per la produzione della Ford Model T. Questo innovativo metodo di produzione rese possibile la realizzazione di automobili in serie a costi accessibili. Ogni operaio era specializzato in una singola mansione ripetitiva, permettendo di assemblare i veicoli in maniera più rapida ed efficiente.
La seconda rivoluzione industriale portò quindi ad una produzione di massa grazie all'automazione dei processi resa possibile dall'elettricità e dalla catena di montaggio. Ciò ebbe un enorme impatto sulla società, con una crescita esponenziale della produzione industriale.
La Terza Rivoluzione Industriale
La terza rivoluzione industriale, nota anche come rivoluzione digitale, è iniziata negli anni '60 ed è stata caratterizzata dall'avvento dell'elettronica, dell'informatica e delle tecnologie dell'automazione.
L'introduzione dei primi computer ha permesso di automatizzare molti processi produttivi, aumentando notevolmente la produttività. Nel giro di pochi decenni, la potenza di calcolo dei computer è cresciuta in modo esponenziale, consentendo applicazioni sempre più sofisticate.
Una svolta cruciale è stata la comparsa dei robot industriali programmabili, in grado di sostituire gli esseri umani nello svolgimento di compiti ripetitivi e pericolosi. La robotica ha rivoluzionato le catene di montaggio, rendendole più veloci, precise ed efficienti.
Altri elementi distintivi di questa rivoluzione sono stati l'avvento di Internet, che ha permesso di connettere macchine e sistemi produttivi, e lo sviluppo di software gestionali come i sistemi ERP per ottimizzare i processi aziendali.
In sintesi, l'automazione digitale ha portato ad una produzione di massa altamente flessibile e personalizzabile, gettando le basi per la successiva rivoluzione industriale.
La Quarta Rivoluzione Industriale
La quarta rivoluzione industriale, conosciuta anche come Industria 4.0, è caratterizzata dall'introduzione di tecnologie all'avanguardia come l'Internet delle Cose (IoT), il Big Data e l'Intelligenza Artificiale (AI) che stanno trasformando il modo di produrre.
L'Internet delle Cose permette la connessione e la comunicazione tra macchinari, sistemi e prodotti lungo l'intera catena del valore. Sensori e sistemi cyber-fisici consentono di raccogliere una grande mole di dati che possono essere analizzati tramite tecniche di Big Data e AI.
L'analisi di questi Big Data genera informazioni che permettono di ottimizzare i processi produttivi in tempo reale. Inoltre, l'AI può essere applicata per attività come la manutenzione predittiva o il controllo qualità.
Grazie all'introduzione di queste tecnologie, nell'Industria 4.0 la produzione diventa più flessibile, efficiente e automatizzata. Si tratta di una trasformazione radicale dei processi industriali che promette di portare a una nuova era della produzione.
Vantaggi dell'Industria 4.0
L'Industria 4.0 porta con sé numerosi vantaggi per le aziende manifatturiere. In particolare, consente di ottenere una maggiore produttività ed efficienza grazie all'integrazione di tecnologie avanzate come l'Internet of Things, il cloud computing, i big data e l'intelligenza artificiale.
L'utilizzo di macchinari e sistemi cyber-fisici interconnessi permette di raccogliere una grande mole di dati lungo tutta la catena del valore. Analizzando questi dati è possibile ottimizzare i processi produttivi in tempo reale, ridurre gli sprechi e i fermi macchina, pianificare la manutenzione predittiva ed aumentare la qualità dei prodotti.
Inoltre, grazie all'automazione spinta e alla collaborazione uomo-macchina è possibile velocizzare le operazioni ripetitive e far concentrare gli operatori sulle attività a maggior valore aggiunto. Questo si traduce in una produzione più rapida, flessibile e customizzabile in base alle richieste dei clienti.
L'Industria 4.0 rappresenta quindi una svolta epocale per incrementare la produttività, ridurre i costi operativi e migliorare la competitività delle aziende manifatturiere.
Sfide dell'Industria 4.0
L'Industria 4.0 porta con sé nuove sfide che le aziende devono affrontare per rimanere competitive. Una delle sfide principali è la necessità di riqualificare la forza lavoro. Con l'introduzione di nuove tecnologie come l'Internet of Things, il cloud computing e l'intelligenza artificiale, molti lavori tradizionali stanno diventando obsoleti. I lavoratori devono acquisire nuove competenze digitali e tecniche per gestire i nuovi sistemi.
Le aziende devono investire nella formazione e nell'aggiornamento del personale per adeguarlo ai cambiamenti tecnologici. Senza le giuste competenze, i lavoratori rischiano di rimanere disoccupati. La riqualificazione è fondamentale per evitare l'obsolescenza delle competenze e mantenere alti livelli di produttività ed efficienza. Le aziende che non investono nella formazione della forza lavoro faticheranno a stare al passo con i concorrenti più innovativi.
La transizione verso l'Industria 4.0 richiede quindi uno sforzo congiunto di aziende, lavoratori e istituzioni per garantire che nessuno venga lasciato indietro. La sfida della riqualificazione può essere vinta solo attraverso la collaborazione e la lungimiranza di tutti gli attori coinvolti.
## Il Ruolo Chiave del Software
Il software gioca un ruolo chiave nell'abilitare la trasformazione digitale delle aziende manifatturiere. La convergenza di tecnologie come Internet of Things (IoT), intelligenza artificiale, cloud computing e big data sta rivoluzionando il settore industriale.
Per sfruttare appieno queste innovazioni, le aziende hanno bisogno di software altamente personalizzato in grado di integrarle efficacemente nei processi aziendali. Il software su misura permette di digitalizzare i processi produttivi, raccogliere ed elaborare una grande mole di dati in tempo reale e ottimizzare le operations attraverso analisi predittive.
Ad esempio, il software custom può connettere macchinari e sensori IoT per monitorare da remoto le performance e rilevare malfunzionamenti. L'intelligenza artificiale può analizzare questi dati per ottimizzare la manutenzione predittiva. Il software su misura svolge un ruolo cruciale nell'integrare e orchestrare queste tecnologie emergenti, permettendo alle aziende di trasformarsi in "fabbriche intelligenti".
Come Sfruttare il Software Su Misura
L'adozione di software personalizzato è fondamentale per sfruttare appieno i vantaggi dell'Industria 4.0. Il software su misura permette di automatizzare i processi, raccogliere ed analizzare grandi quantità di dati in tempo reale e ottimizzare le operazioni aziendali.
L'automatizzazione resa possibile dal software customizzato aumenta l'efficienza e la produttività, riducendo gli errori umani ed i tempi di inattività. I processi ripetitivi possono essere delegati al software, liberando risorse umane per attività a maggior valore aggiunto.
La raccolta dati in tempo reale attraverso sensori e dispositivi IoT fornisce informazioni preziose per prendere decisioni data-driven. Il software personalizzato può elaborare questi big data, individuare modelli e trend ed effettuare analisi predittive.
Ciò consente di ottimizzare le operazioni in base ai dati raccolti, ad esempio pianificando meglio la manutenzione predittiva o adeguando la produzione alla domanda. Il software su misura integra e orchestra i vari sistemi aziendali, permettendo un controllo end-to-end di tutti i processi.
In sintesi, il software personalizzato è la chiave per sfruttare appieno le tecnologie abilitanti di Industria 4.0 e trasformare un'azienda in una Fabbrica Digitale altamente efficiente, produttiva e capace di innovazione continua. Investire in software custom è fondamentale per qualsiasi impresa che voglia essere competitiva nell'era dell'Industria 4.0.
Conclusioni
L'Industria 4.0 rappresenta una rivoluzione nel modo di concepire la produzione industriale, con enormi potenzialità in termini di efficienza, produttività e sostenibilità. Tuttavia, per sfruttare appieno queste opportunità è necessario un cambio di mentalità sia da parte delle aziende che dei lavoratori.
Il ruolo del software su misura è fondamentale in questa transizione. Consente di digitalizzare i processi produttivi e integrarli perfettamente con le nuove tecnologie come IoT, big data analytics, AI. Ma per essere davvero efficace, il software deve essere progettato intorno alle specifiche esigenze dell'azienda.
In sintesi, per cogliere i benefici dell'Industria 4.0, le aziende devono investire in competenze, formazione del personale e software customizzato. Solo così si può ottenere un reale vantaggio competitivo. L'approccio vincente è puntare sull'integrazione tra persone e tecnologie, facendo leva sul know-how interno all'impresa.
Parliamo del tuo progetto?
Non aspettare: ogni grande progetto inizia da una conversazione. Contattaci per scoprire come possiamo aiutarti.